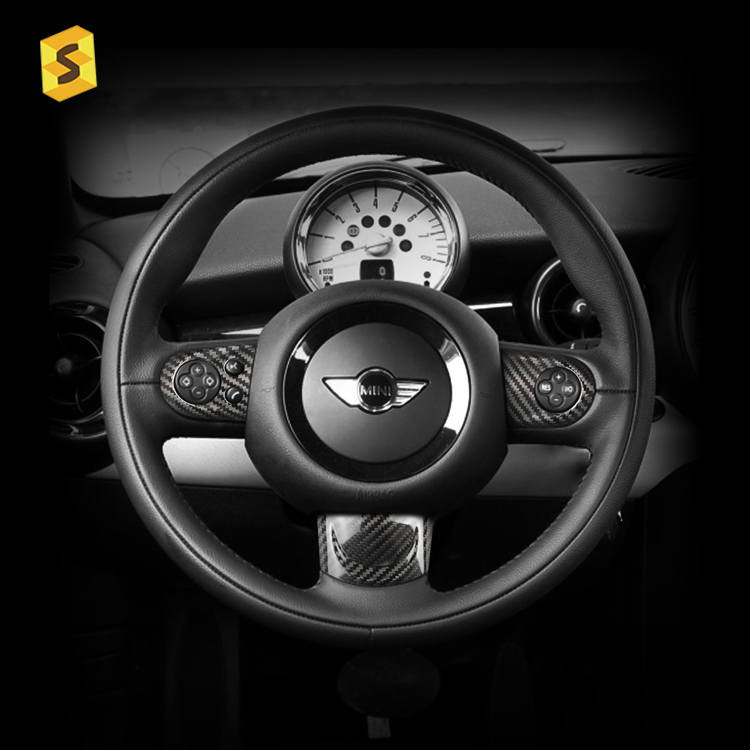
Autoteile aus Kohlefaser werden in der Automobilindustrie zunehmend eingesetzt, da sie außergewöhnliches Verhältnis von Festigkeit zu Gewicht, verbesserte Aerodynamik und ästhetisches Erscheinungsbild. Automobilhersteller nutzen Autoteile aus Kohlefaser für das Außen- und Innendesign, um die Leistung und das Aussehen ihrer Fahrzeuge zu verbessern.
Die Verwendung von Autoteile aus Kohlefaser im Außenbereich Designkomponenten wie Motorhauben, Spoiler und Kotflügel haben einen erheblichen Einfluss auf die Leistung eines Fahrzeugs. Da die Verwendung von Kohlefaser-Autoteilen immer weiter zunimmt, ist es wichtig zu verstehen, Herstellungsprozess verwendet, um sie zu erstellen.
Schritt #1: Materialbeschaffung
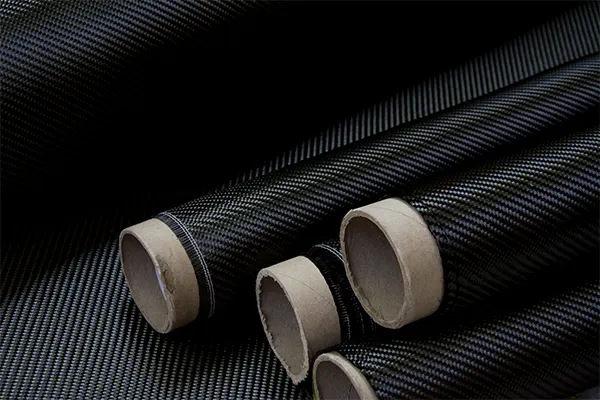
Kohlenstofffasern bestehen aus mikroskopisch kleinen Fasern, die dünner als ein menschliches Haar und bestehen hauptsächlich aus Kohlenstoffatomen. Diese Fasern werden mit einem Harzsystem wie Epoxid, Phenol oder Polyurethan kombiniert, um ein stark und leicht Verbundwerkstoff.
Die Qualität der im Herstellungsprozess verwendeten Rohstoffe ist entscheidend für die Qualität des Endprodukts. Stärke und HaltbarkeitSelbst kleine Abweichungen in der Qualität des Harzsystems oder der Konsistenz der Kohlefaserplatten können die Gesamtqualität und Leistung des fertigen Produkts erheblich beeinträchtigen.
Für den Herstellungsprozess werden außerdem Hilfsstoffe benötigt, wie Trennmittel, Härter und Produkte zur Formvorbereitung. Diese Materialien ermöglichen die Herstellung hochwertiger Autoteile aus Kohlefaser, die den Industriestandards hinsichtlich Festigkeit, Haltbarkeit und Aussehen entsprechen.
Durch die Verwendung hochwertige Rohstoffe Indem sie sich bei der Herstellung von Autoteilen aus Kohlefaser auf erfahrene Hersteller verlassen, können Automobilhersteller sicherstellen, dass ihre Produkte die Industriestandards erfüllen oder übertreffen und die von den Kunden gewünschte Leistung und Ästhetik bieten.
Schritt #2: Design und Formen
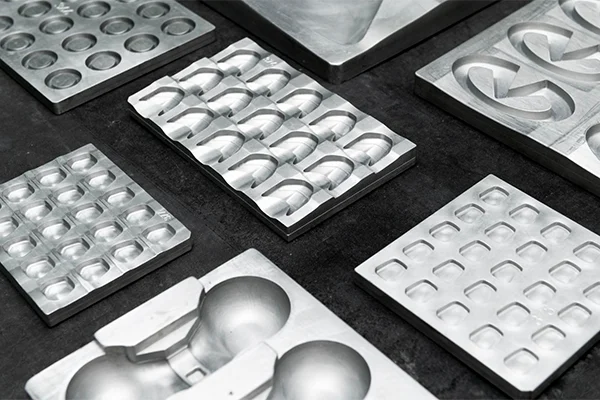
Der Design- und Formprozess für Kohlefaser-Autoteile beginnt mit der Erstellung präziser Formen, die zur Herstellung der Teile verwendet werden. Die Formen bestehen typischerweise aus Materialien wie Aluminium, Stahl oder Verbundwerkstoff die langlebig sind und den im Produktionsprozess erforderlichen hohen Temperaturen und Drücken standhalten.
Präzision und Genauigkeit im Formenbau sind entscheidend, um sicherzustellen, dass die Carbonfaser-Autoteile den korrekten Spezifikationen entsprechen. Abweichungen von den gewünschten Abmessungen der Form können zu unerwünschten Verformungen der fertigen Teile führen und deren Qualität und Leistung beeinträchtigen.
Sobald die Formen fertig sind, werden Kohlefaserplatten darauf ausgelegt und zugeschnitten. Anschließend werden die Kohlefaserplatten übereinander geschichtet und mit einem Harzsystem getränkt. Die Schichten können in verschiedene Richtungen ausgerichtet werden, um Teile mit unterschiedlichen Festigkeits- und Steifigkeitseigenschaften zu erzeugen.
Um sicherzustellen, dass sich die Kohlefaserplatten gut an die Formen anpassen und vollständig mit dem Harz durchtränkt werden, werden sie oft vakuumverpackt. Die Vakuumbeutel tragen dazu bei, den Druck gleichmäßig über die gesamte Oberfläche der Kohlefaser zu verteilen, was zu gleichmäßigeren und qualitativ hochwertigeren Teilen führt.
Schritt #3: Prepreg-Stadium
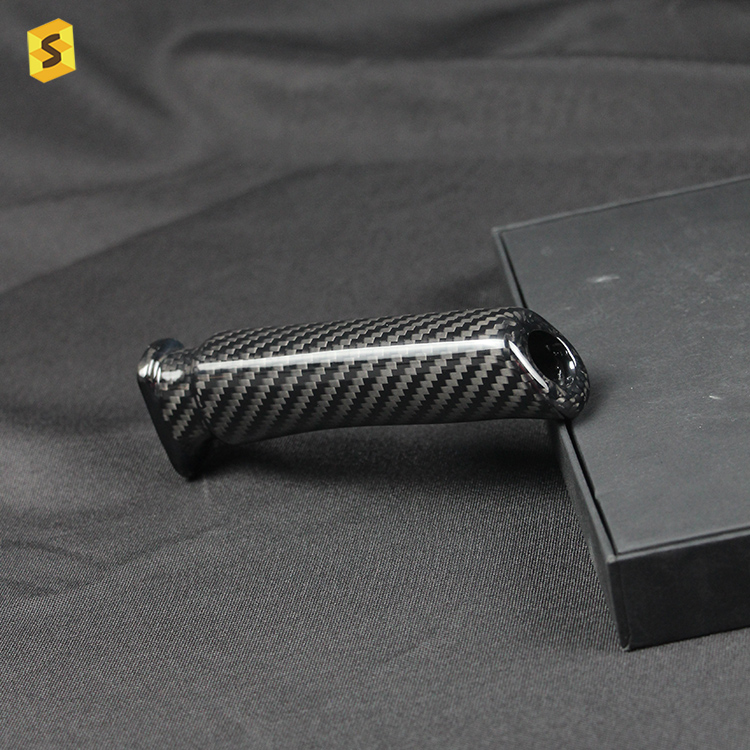
Während der Prepreg-Phase des Herstellungsprozesses von Kohlefaser-Autoteilen wird Harz verteilt und die Kohlefaser verstärkt. Dieser Prozess beinhaltet Kombination der Kohlenstofffaser mit einem Harzsystem, wie beispielsweise Epoxidharz, um ein starkes und haltbares Verbundmaterial zu schaffen.
Der Prepreg-Prozess kann durchgeführt werden von Hand oder mit Spezialmaschinen.
- Bei manueller AusführungZunächst wird Harz auf die Kohlefaserplatten aufgetragen. Anschließend werden diese geschichtet und gerollt, um eine gleichmäßige Harzverteilung zu gewährleisten. Die harzbeschichtete Kohlefaser wird anschließend zugeschnitten und in eine Form gelegt.
- Beim Einsatz von SpezialmaschinenDie Kohlefaser wird durch eine Maschine geführt, die das Harz gleichmäßig auf die Platte aufträgt. Die harzbeschichtete Kohlefaser kann dann zugeschnitten und in die Form eingelegt werden, ohne dass ein manuelles Rollen erforderlich ist.
Während der Prepreg-Phase ist es wichtig, dass die richtige Menge Harz wird auf die Kohlefaser aufgetragen, um sicherzustellen, dass sie vollständig durchdrungen und verstärkt ist. Wenn es zu wenig Harz aufgetragen, kann der Verbundwerkstoff zu spröde und anfällig für Risse sein. Andererseits wenn zu viel Harz verwendet wird, kann sich das Gewicht des Endprodukts erhöhen, was die Vorteile der Gewichtsreduzierung durch die Verwendung von Kohlefaser beeinträchtigen kann.
Um sicherzustellen, dass hochwertige Carbonfaser-Autoteile hergestellt werden, Hersteller Es muss ein Gleichgewicht zwischen dem Auftragen der richtigen Harzmenge und der Sicherstellung einer gleichmäßigen Verteilung gefunden werden.
Schritt #4: Bildung und Aushärtung
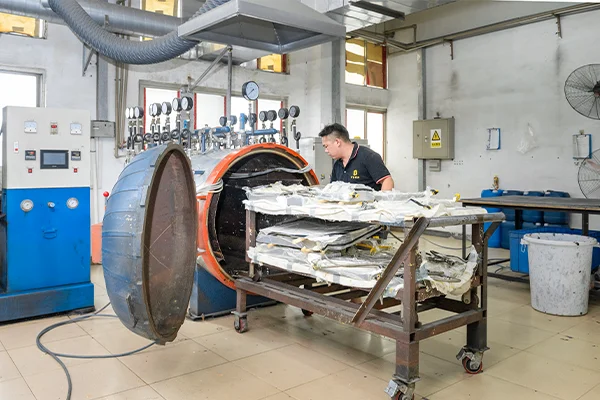
In der Formungs- und Aushärtungsphase des Herstellungsprozesses von Kohlefaser-Autoteilen wird das Kohlefasermaterial in seine endgültige Form gebracht und anschließend ausgehärtet, um einen starken und langlebigen Verbundwerkstoff zu erzeugen.
Der Entstehungsprozess umfasst Platzieren des Kohlefasermaterials, die mit Harz beschichtet ist, in eine Form. Der Prozess erfordert Präzision und Genauigkeit, um sicherzustellen, dass die Kohlefaser genau den Abmessungen der Form entspricht. Um sicherzustellen, dass die Kohlefaser an Ort und Stelle bleibt und der Druck gleichmäßig verteilt wird, Vakuumverpackung wird häufig verwendet.
Beim Vakuumverpacken wird ein Beutel über die Form gelegt und um das Kohlefasermaterial herum angeordnet, die Luft wird aus dem Beutel abgesaugt, um ein Vakuum zu erzeugen, und während des Aushärtungsprozesses wird gleichmäßiger Druck auf die gesamte Oberfläche des Teils ausgeübt, was zu hochwertig Autoteile aus Kohlefaser mit gleichbleibender Dichte und Festigkeit.
Der Aushärtungsprozess ist für die Herstellung hochwertiger Autoteile aus Kohlefaser von entscheidender Bedeutung. Aushärtezeit, Temperatur und Druck muss sorgfältig überwacht und kontrolliert werden, um sicherzustellen, dass das Harz vollständig ausgehärtet und die Kohlefaser richtig verstärkt ist. Temperatur und Druck werden üblicherweise stufenweise angewendet, zunächst mit niedriger Hitze und niedrigem Druck, um die verbleibende Luft zu entfernen, und anschließend mit hoher Hitze und hohem Druck, um den Aushärtungsprozess abzuschließen.
Die Qualität und Leistung des Endprodukts hängen maßgeblich von der Genauigkeit des Aushärtungsprozesses ab. Bei unsachgemäßer Aushärtung können die Kohlefaser-Autoteile spröde, schwach oder anfällig für Verformungen oder Risse sein.
Schritt #5: Trimmen und Schneiden
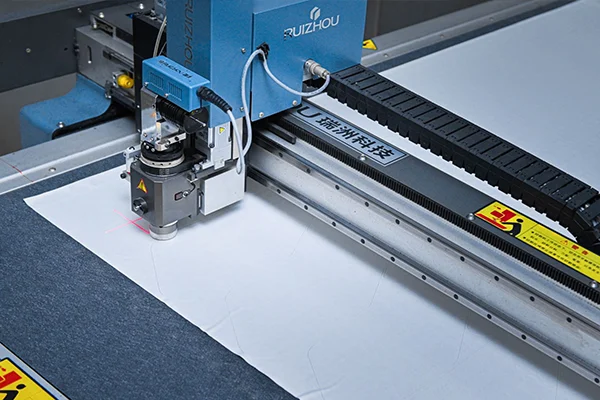
Nachdem die Autoteile aus Kohlefaser geformt und ausgehärtet wurden, müssen sie zugeschnitten und geschnitten werden, um die gewünschte Größe und Form zu erreichen. Trimmen und Schneiden sind kritische Schritte im Herstellungsprozess, da sie das Gewicht, die Festigkeit und die Ästhetik des Endprodukts beeinflussen können.
Der Trimm- und Schneideprozess umfasst typischerweise mit CNC-Maschinen oder Handwerkzeugen, wie Sägen oder Scheren, um die Kohlefaser-Autoteile präzise auf ihre endgültige Form und Größe zuzuschneiden. Der Prozess kann jedoch aufgrund der Sprödigkeit der Kohlefaser eine Herausforderung darstellen, was bedeutet, dass präzise Schnitte erforderlich sind, um ein Splittern oder Brechen des Materials zu vermeiden.
Präzision ist besonders wichtig beim Trimmen und Schneiden von Kohlefaser-Autoteilen, da selbst eine geringfügige Abweichung von der gewünschten Größe und Form die Leistung und das Aussehen des Teils beeinträchtigen kann. Zum Beispiel wenn ein Teil zu groß ist, passt es möglicherweise nicht richtig, was die Montage des Endprodukts beeinträchtigt. Andererseits wenn ein Bauteil zu klein ist, bietet es möglicherweise nicht das erforderliche Maß an Unterstützung, was dazu führen kann, dass die Struktur mit der Zeit schwächer wird oder versagt.
Da Autoteile aus Kohlefaser oft aus ästhetischen Gründen verwendet werden, kann ein unzureichendes Zuschneiden oder Schneiden die Optik des Teils beeinträchtigen. Unvollkommenheiten, wie z. B. raue Kanten, können die Gesamtqualität des Produkts beeinträchtigen und sich negativ auf die Kundenzufriedenheit auswirken.
Schritt #6: Qualitätskontrolle
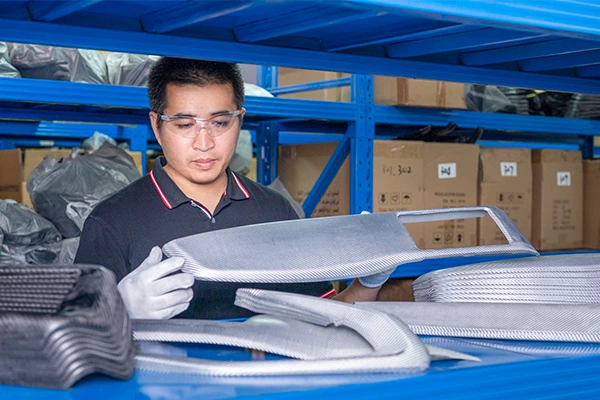
Die Qualitätskontrolle ist ein wesentlicher Aspekt des Herstellungsprozesses von Kohlefaser-Autoteilen. Sie hilft, Mängel oder Unvollkommenheiten vor der Freigabe des Endprodukts zu erkennen und stellt sicher, dass die Kunden qualitativ hochwertige Teile erhalten.
Während des gesamten Herstellungsprozesses werden Qualitätskontrolltests durchgeführt, um sicherzustellen, dass die Carbonfaser-Autoteile ordnungsgemäß geformt und ausreichend verstärkt sind. Im Folgenden sind einige der am häufigsten angewandten Qualitätskontrolltests aufgeführt:
- Visuelle Inspektion: Dieser Test ist notwendig, um Oberflächenfehler oder Mängel zu erkennen, die mit bloßem Auge nicht erkennbar sind, wie beispielsweise Risse und Blasen.
- Ultraschallprüfung: Bei diesem Test werden Schallwellen verwendet, um die Integrität des Verbundmaterials zu bewerten.
- Röntgenprüfung: Bei diesem Test wird die innere Struktur des Verbundmaterials in Bereichen, in denen eine visuelle Inspektion schwierig ist, mithilfe von Röntgenstrahlen überprüft.
- Thermische Prüfung: Dieser Test ermittelt die Fähigkeit des Verbundmaterials, hohen Temperaturen standzuhalten und gibt Aufschluss über die Vollständigkeit der Aushärtung.
- Zug- und Druckprüfungen: Diese Tests bewerten die Festigkeit und Haltbarkeit des Verbundmaterials und identifizieren Mängel in seiner Konstruktion.
Die Art der Qualitätsprüfungen hängt von den Spezifikationen der Kohlefaser-Autoteile und den Anforderungen des Herstellers ab. Die Prüfhäufigkeit wirkt sich auch auf die Qualität des Endprodukts aus. Hochfrequenzprüfungen sind effektiver, um Defekte frühzeitig zu erkennen.
Schritt #7: Endkontrolle und Verpackung
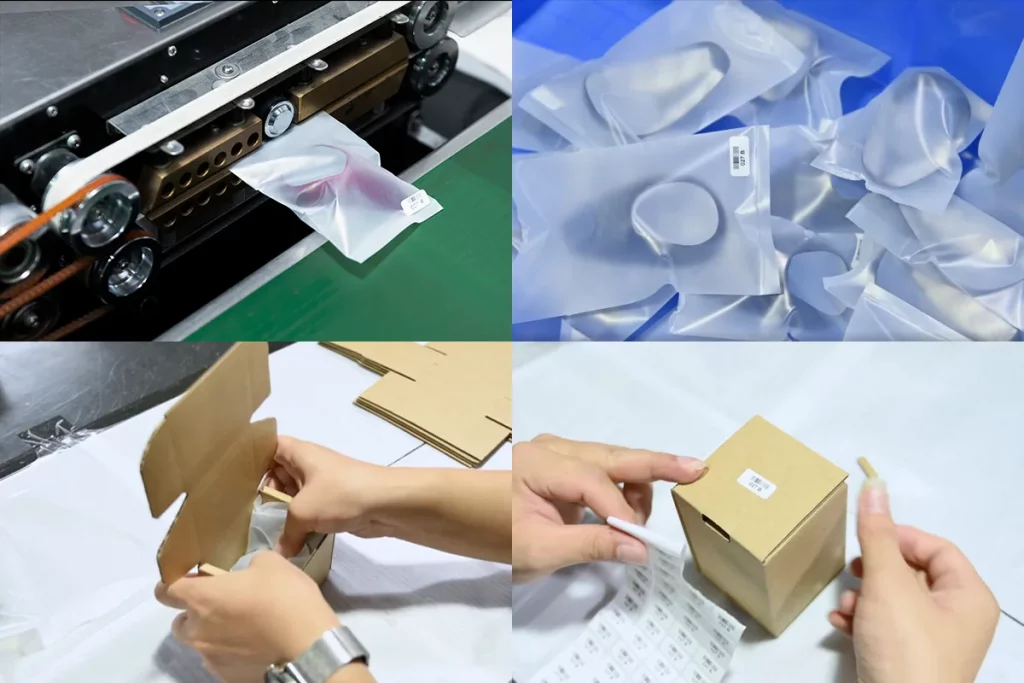
Der abschließende Inspektionsprozess stellt sicher, dass die Autoteile aus Kohlefaser keine Mängel aufweisen und die erforderlichen Spezifikationen erfüllen.
Visuelle Inspektion
Dieser Prozess beinhaltet typischerweise eine Sichtprüfung Dabei wird das Endprodukt mit dem ursprünglichen Entwurf oder den Auftragsspezifikationen verglichen. Es können auch andere Prüfmethoden eingesetzt werden, wie z. B. Ultraschall- oder Wärmeprüfung, um sicherzustellen, dass das Verbundmaterial frei von Struktur- und Oberflächenfehlern ist. Sobald die Kohlefaserteile die Endkontrolle bestanden haben, sind sie bereit für die Verpackung.
Richtige Verpackung
Eine ordnungsgemäße Verpackung ist unerlässlich, um Kohlefaser-Autoteile während Transport und Lagerung zu schützen. Die Teile werden typischerweise mit Schutzmaterialien verpackt, wie z. B. Schaumstoff, Luftpolsterfolie oder Karton, um Transportschäden zu vermeiden. Die verwendete Verpackung wird in der Regel unter Berücksichtigung der Transportmethode ausgewählt. Beispielsweise gelten für Flugzeuge weniger strenge Verpackungsanforderungen als für Landfahrzeuge.
Labels
Etiketten mit Kundeninformationen, Produktidentifikationscodes und Barcodes können der Verpackung hinzugefügt werden. Diese Etiketten helfen bei der Identifizierung der Teile im Bestandsmanagement und unterstützen den Sendungsverfolgungs- und Versandprozess.
Lieferung
Abschließend werden die Carbonfaser-Autoteile für den Versand vorbereitet. Die Abwicklung des Versands wird sorgfältig mit den Reedereien abgestimmt, um sicherzustellen, dass die Produkte ohne Verzögerung und Beschädigung ihren Bestimmungsort erreichen. Carbonfaser-Autoteile werden häufig an Automobilhersteller, Händler oder direkt an Kunden geliefert, die kundenspezifische Teile bestellt haben.
Abschluss
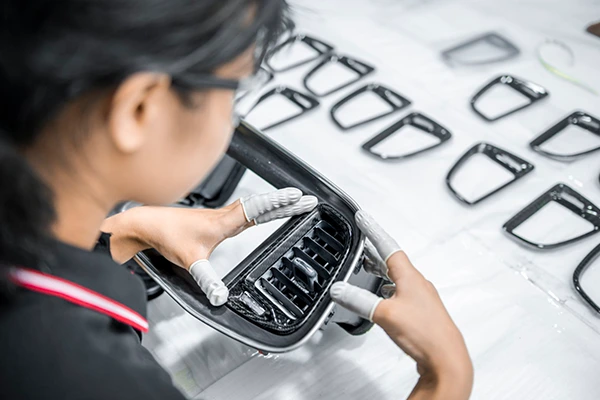
Zusammenfassend lässt sich sagen, dass der Herstellungsprozess von Autoteilen aus Kohlefaser ein komplexer und sorgfältiger Prozess ist, der mehrere Phasen umfasst, darunter Materialauswahl, Laminieren, Aushärten, Trimmen und Schneiden, Qualitätskontrolle sowie Endkontrolle und Verpackung. Jeder Schritt muss mit Präzision und Genauigkeit ausgeführt werden, um qualitativ hochwertige Produkte zu gewährleisten, die den gewünschten Spezifikationen entsprechen.
Autoteile aus Kohlefaser sind ein wichtiger Bestandteil des modernen Automobildesigns und bieten einzigartige Eigenschaften, die die Leistung, Sicherheit und Ästhetik des Fahrzeugs verbessern. Die Zukunft von Kohlefaser-Autoteilen in der Automobilindustrie ist vielversprechend, und es ist zu erwarten, dass immer mehr Automobilhersteller dieses Material in ihren Produkten einsetzen werden.