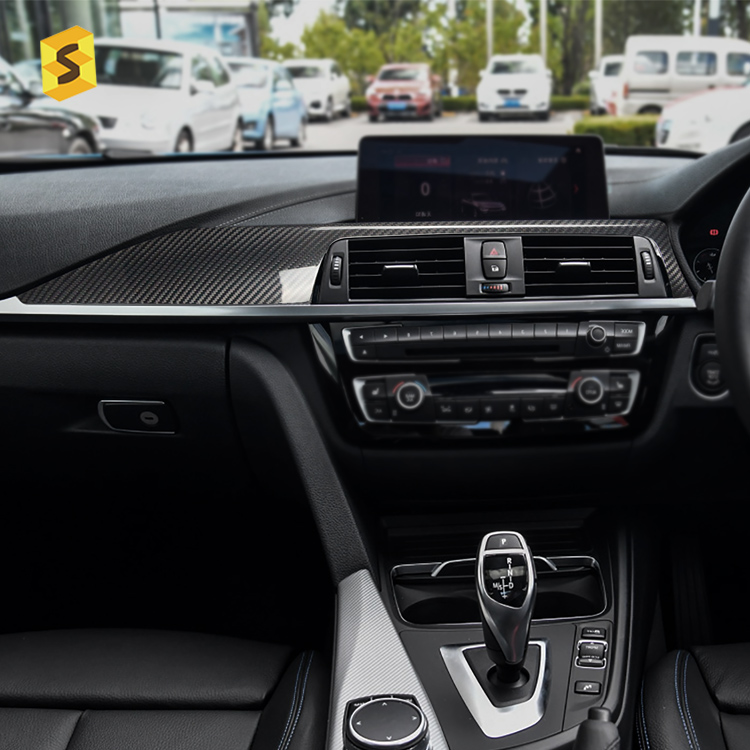
자동차 산업은 탄소 섬유를 획기적인 소재로 꾸준히 수용해 왔습니다. 뛰어난 강도 대 중량 비율탄소 섬유는 자동차 제조의 미래를 혁신할 엄청난 잠재력을 자랑합니다. 이 가볍고 고성능 소재는 자동차의 설계, 제작, 그리고 운전 방식에 혁명을 일으킬 힘을 가지고 있습니다.
이 글에서는 자동차 산업에서 탄소 섬유 자동차 부품의 중요성을 살펴보고, 미래 자동차 발전에 미칠 잠재적 영향을 심층적으로 분석합니다. 탄소 섬유가 어떻게 혁신을 주도하고 우리가 운전하는 자동차의 개념을 새롭게 정의할 수 있을지 확인해 보세요.
자동차 산업에서 탄소 섬유의 현재 사용
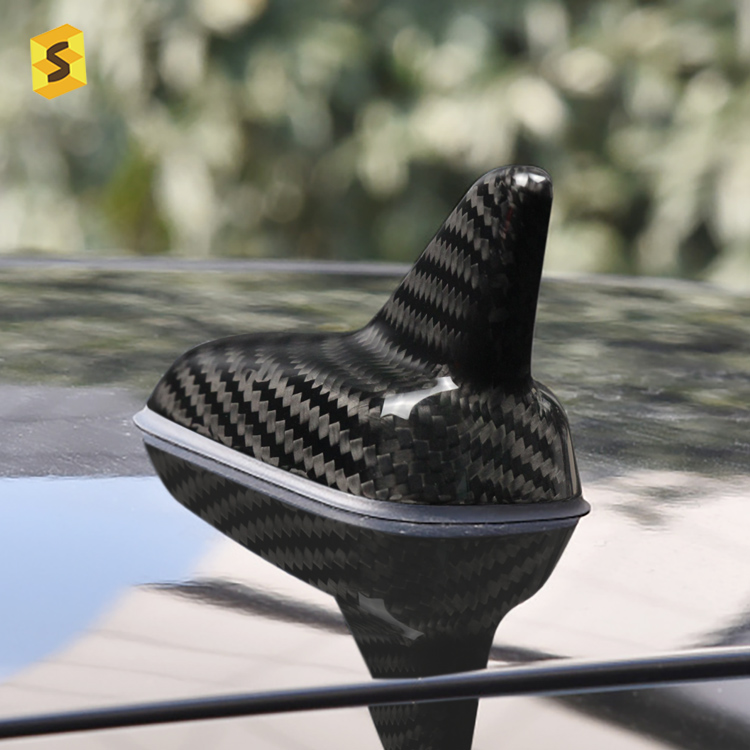
탄소 섬유는 이미 자동차 산업에 상당한 진출을 이루었습니다. 조작탄소 섬유는 다양한 부품과 시스템에 적용 가능합니다. 탄소 섬유의 현재 용도와 자동차 산업에 미치는 이점을 자세히 살펴보겠습니다.
차체 패널 및 구조
탄소 섬유는 후드, 루프, 도어, 펜더 등 자동차 차체 패널 제조에 널리 사용됩니다. 높은 강도 대 중량비 덕분에 가볍지만 견고한 차체 구조를 구현할 수 있으며, 이를 통해 연비, 민첩성, 그리고 성능이 향상됩니다. 탄소섬유 외장 부품 또한 무게 분포를 최적화하여 소음 감소와 핸들링 개선에도 기여합니다.
섀시 및 서스펜션 구성 요소
탄소 섬유는 서브프레임, 컨트롤 암, 서스펜션 링크와 같은 섀시 구성 요소를 생산하는 데 사용됩니다. 탄소 섬유를 활용함으로써 자동차 제조업체는 스프링 아래 무게를 줄이고 반응성, 안정성, 그리고 승차감을 향상시킬 수 있습니다. 탄소 섬유의 강성은 핸들링을 향상시켜 정확하고 예측 가능한 차량 동역학을 제공합니다.
내부 및 트림 구성 요소
탄소섬유 내장 부품 차량 내부에 우아함과 스포티함을 더해주며 종종 사용됩니다. 내부 트림 패널센터 콘솔, 대시보드 액센트 등 다양한 요소에 적용됩니다. 탄소 섬유는 미적인 아름다움 외에도 품질이나 안전 기준을 저해하지 않으면서도 차량 무게를 줄이는 데 기여합니다. 가벼운 내부 요소는 차량의 전반적인 균형을 개선하고 에너지 소비를 줄이는 데 기여합니다.
성능 향상
탄소 섬유는 고성능 스포츠카와 슈퍼카에 널리 사용되어 속도와 민첩성을 극대화합니다. 탄소 섬유 부품을 통합함으로써 차량의 출력 대 중량비를 높여 폭발적인 가속력과 탁월한 핸들링을 구현할 수 있습니다. 스포일러, 디퓨저, 공기역학 부품과 같은 성능 중심 부품은 탄소 섬유의 강도와 가벼운 무게 덕분에 이점을 누릴 수 있습니다.
탄소 섬유 자동차 부품을 사용하면 성능 향상 외에도 다음과 같은 이점이 있습니다.
- 무게 감소 및 연비
탄소 섬유의 가벼운 특성은 차량 무게를 줄여 연비를 향상시키고 배기가스 배출량을 줄입니다. 차량이 가벼울수록 추진력도 줄어들어 더욱 친환경적인 교통수단으로 거듭날 수 있습니다.
- 강도와 내구성
탄소 섬유는 뛰어난 강도를 자랑하여 충격, 진동, 부식에 대한 내성이 매우 뛰어납니다. 탄소 섬유로 제작된 자동차 부품은 혹독한 환경을 견뎌낼 수 있어 수명과 신뢰성을 보장합니다.
- 향상된 디자인 가능성
탄소 섬유의 유연성과 성형성은 정교하고 독특한 디자인을 가능하게 하여 자동차 제조업체들이 시각적으로 눈길을 끄는 차량을 제작할 수 있도록 합니다. 탄소 섬유를 사용하면 맞춤형 미적 감각을 구현할 수 있어 자동차 애호가들이 자신의 차량을 개인화할 수 있습니다.
탄소 섬유가 지속적으로 발전하고 진화함에 따라 자동차 산업에서 탄소 섬유의 사용이 증가함에 따라 가볍고 지속 가능하며 고성능의 차량이 표준이 되는 혁신적인 미래가 다가오고 있습니다.
탄소 섬유 기술의 발전
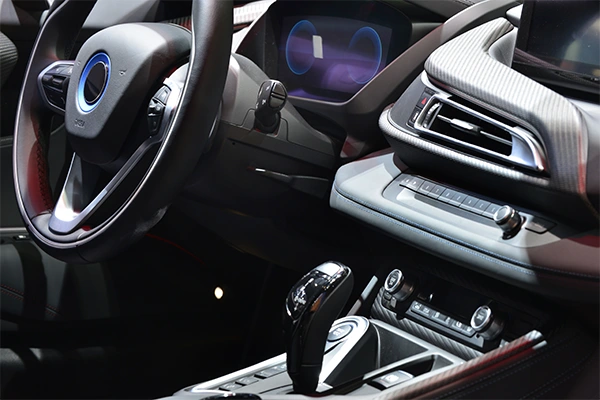
탄소 섬유 기술은 제조 기술과 재료 특성 모두에서 상당한 발전을 이루었습니다. 이러한 발전은 자동차 제조 분야에서 탄소 섬유 도입을 촉진하고 미래 혁신의 토대를 마련하고 있습니다. 탄소 섬유 기술의 최신 동향을 살펴보겠습니다.
개선된 제조 기술
새로운 제조 공정은 탄소 섬유 생산에 혁명을 일으켜 효율성 향상과 비용 절감을 가져오고 있습니다. 주요 기술은 다음과 같습니다.
- 자동 광섬유 배치(AFP)
AFP는 로봇 시스템을 활용하여 탄소 섬유 가닥을 정밀하게 배치하여 복잡한 형상과 구조물을 높은 정확도로 제작할 수 있도록 합니다. 이러한 자동화된 공정은 재료 사용량을 최적화하고 낭비를 줄이며 생산 속도를 높입니다.
- 수지 전사 성형(RTM)
RTM은 미리 성형된 탄소 섬유 매트에 수지를 주입하여 정밀하고 일관된 복합 부품을 제작하는 공정입니다. 이 공정은 수지 주입 제어를 향상시켜 공극이 적고 강도가 향상된 고품질 부품을 생산합니다.
- 연속 섬유 제조(CFM)
CFM은 탄소 섬유 시트 또는 테이프를 연속적으로 생산하여 직조와 같은 중간 단계가 필요 없습니다. 이 방식은 생산 속도를 높이고, 폐기물을 줄이며, 확장성을 향상시킵니다.
향상된 재료 특성
연구자들과 제조업체들은 탄소 섬유 복합재의 한계를 끊임없이 넓혀가며 재료 특성 개선에 집중하고 있습니다. 다음과 같은 분야에서 상당한 발전이 이루어졌습니다.
- 더 높은 강도 대 중량 비율
엔지니어들은 강철이나 알루미늄과 같은 기존 소재의 성능을 뛰어넘는, 더욱 높은 강도 대 중량비를 가진 탄소 섬유 복합재를 개발하고 있습니다. 이러한 첨단 복합재는 가벼운 외관을 유지하면서도 뛰어난 강도를 제공하여 차량의 추가적인 중량 감소를 가능하게 합니다.
- 향상된 충격 저항성
탄소 섬유 복합재는 충격에 대한 내구성이 점점 더 향상되어 안전이 중요한 자동차 부품에 이상적인 소재로 자리매김하고 있습니다. 첨단 제조 기술과 소재 배합을 통해 탄소 섬유는 이제 충격력을 더 잘 흡수하고 분산시켜 차량 안전성을 향상시킵니다.
- 향상된 유연성과 내구성
탄소 섬유 기술의 혁신으로 유연성과 내구성이 향상된 복합재가 개발되었습니다. 이러한 유연성 덕분에 복잡한 형상과 곡면에 쉽게 통합할 수 있어 설계 가능성이 더욱 넓어졌습니다. 향상된 내구성은 탄소 섬유 부품의 수명을 보장하여 까다로운 자동차 응용 분야에서 장기간 사용하기에 적합합니다.
제조 기술과 소재 특성의 이러한 발전은 자동차 산업에서 탄소 섬유의 광범위한 채택을 촉진합니다. 탄소 섬유가 계속해서 발전함에 따라, 우리는 경량, 고성능, 지속 가능한 자동차의 미래를 주도할 더욱 흥미로운 발전을 기대할 수 있습니다.
자동차에 대한 탄소 섬유의 미래 응용
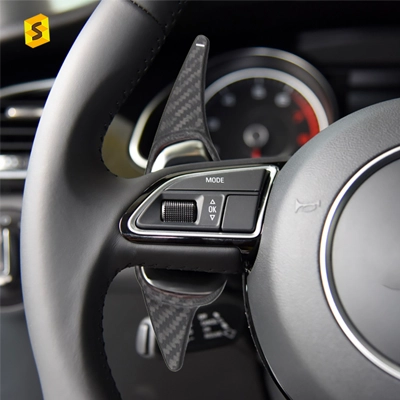
탄소 섬유는 자동차의 미래를 형성하는 데 중요한 역할을 할 것으로 예상됩니다. 탄소 섬유 기술이 지속적으로 발전함에 따라 그 응용 분야가 확대되어 자동차 산업에 다양한 방식으로 혁신을 가져올 것으로 예상됩니다.
효율성 향상을 위한 경량화
탄소 섬유의 주요 이점 중 하나는 차량 무게를 크게 줄여 연비와 성능을 향상시킬 수 있다는 것입니다. 향후 탄소 섬유는 다음과 같은 용도로 사용될 수 있습니다.
- 기존 내연 기관의 무게를 더욱 줄여 전반적인 효율성을 높이고 탄소 배출량을 줄입니다.
- 전기 및 하이브리드 자동차에 대한 상당한 잠재력을 보유하고 있으며, 무거운 배터리의 무게를 상쇄하여 주행거리를 늘릴 수 있습니다.
- 질량이 감소하여 가속이 빨라지고 핸들링이 향상되었습니다.
안전 혁신
탄소 섬유는 뛰어난 강도와 내충격성을 갖춰 차량 안전 강화에 이상적인 소재입니다. 향후 다음과 같은 분야에 적용될 수 있습니다.
- 승객실과 충격 흡수 구역 등 중요한 부분에 탄소 섬유 부품을 사용하여 충돌 안전성을 향상시켰습니다.
- 탄소 섬유가 충격력을 흡수하고 재분배하여 부상 위험을 줄여 탑승자 보호가 강화되었습니다.
- 탄소 섬유 보강 기술의 발전으로 구조적 무결성이 강화되어 차량에 대한 견고한 안전 프레임워크를 제공할 수 있습니다.
디자인의 자유와 맞춤화
탄소 섬유는 비교할 수 없는 디자인 자유도를 제공하여 독특한 자동차 디자인과 맞춤형 미적 감각을 구현할 수 있습니다. 향후 다음과 같은 분야에 적용될 수 있습니다.
- 차체 패널에 탄소 섬유를 통합하여 이전에는 구현하기 어려웠던 혁신적인 모양, 곡선 및 윤곽을 구현할 수 있게 되었습니다.
- 개인화된 구성품에 대한 기회를 통해 자동차 애호가들은 탄소 섬유 악센트, 트림 및 세부 사항으로 차량을 맞춤 설정할 수 있습니다.
- 탄소 섬유의 본질적인 아름다움은 차량의 전반적인 시각적 매력을 향상시켜 세련미와 스포티함을 더해줍니다.
자동차에 탄소 섬유를 적용하는 미래는 업계를 혁신할 엄청난 잠재력을 지니고 있습니다. 효율성 향상을 위한 경량화부터 안전 혁신 및 디자인 자유도 향상에 이르기까지, 탄소 섬유는 연비와 안전성을 향상시킬 뿐만 아니라 시각적으로 매력적이고 맞춤형 디자인까지 갖춘 차량 개발을 주도할 것입니다. 연구 개발이 계속됨에 따라, 자동차 산업에서 탄소 섬유가 핵심 소재로서 확고한 입지를 굳건히 할 획기적인 발전이 기대됩니다.
과제와 한계
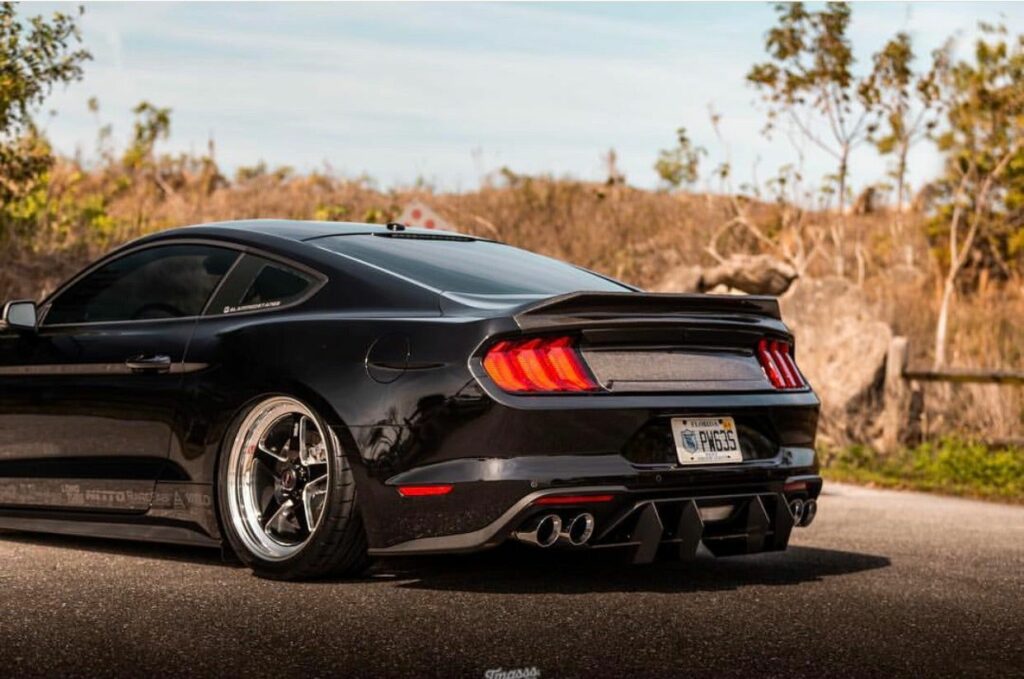
출처: 핀터레스트
자동차를 포함한 다양한 산업 분야에서 탄소 섬유의 광범위한 도입은 해결해야 할 몇 가지 과제와 한계에 직면해 있습니다. 이러한 과제와 한계는 다음과 같습니다.
비용
탄소 섬유는 강철이나 알루미늄과 같은 기존 소재에 비해 여전히 상대적으로 비쌉니다. 원자재, 제조 및 가공 비용이 높아 전체 비용이 증가하기 때문입니다. 그러나 제조 기술의 발전, 규모의 경제, 그리고 경쟁 심화로 인해 비용이 점차 낮아지고 있습니다.
생산 능력
현재 탄소 섬유 생산 능력은 제한적입니다. 증가하는 수요를 충족하기 위해 생산량을 늘리려면 제조 시설과 장비에 대한 상당한 투자가 필요합니다. 탄소 섬유의 접근성과 비용 효율성을 높이기 위해서는 생산 능력 증대가 필수적입니다.
재활용
탄소 섬유는 재활용 측면에서 어려움을 겪습니다. 복잡한 복합 구조와 탄소 섬유를 수지에서 분리해야 하는 필요성 때문에 재활용은 기술적으로 어렵고 비용이 많이 드는 과정입니다. 탄소 섬유 부품의 수명 주기 지속가능성을 개선하기 위해서는 재활용 방법을 개선하고 더욱 지속 가능한 수명 종료 솔루션을 개발하는 것이 필수적입니다.
규제 고려 사항
자동차에 탄소 섬유를 도입하는 것 역시 규제 측면에서 고려해야 할 사항입니다. 안전, 충돌 안전성, 배출가스 및 방화 관련 규정은 탄소 섬유 부품에 대한 추가적인 검증 및 시험을 요구할 수 있습니다. 이러한 규정을 준수하는 것은 탄소 섬유의 광범위한 도입을 위해 매우 중요합니다.
이러한 과제와 한계를 해결하려면 업계, 연구 기관, 규제 기관 간의 협력이 필요합니다. 제조 공정 개선을 위한 연구 개발 투자, 대체 및 지속 가능한 원자재 탐색, 그리고 효율적인 재활용 방법 개발이 핵심적인 과제입니다. 또한, 탄소 섬유 도입에 적합한 표준 및 지침을 수립하기 위해 규제 당국과 적극적으로 소통하는 것도 중요합니다.
이러한 과제를 극복함으로써 자동차 산업에서 탄소 섬유의 수용이 더욱 확대되고, 주류 자동차 생산에의 통합이 촉진될 것입니다. 기술 발전이 지속됨에 따라 탄소 섬유의 비용 효율성, 생산 능력, 재활용성, 그리고 규제 준수성이 향상되어, 탄소 섬유의 채택이 더욱 확대되고 그 잠재력이 최대한 발휘될 것으로 예상됩니다.
협력 및 파트너십
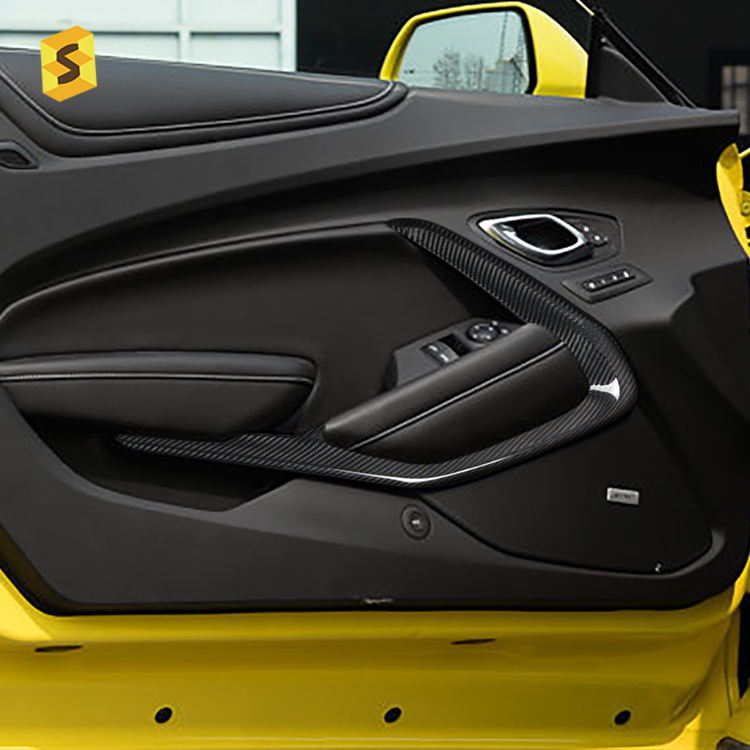
자동차 제조업체, 공급업체 및 탄소 섬유 자동차 부품 제조업체 자동차 산업에서 탄소 섬유의 도입과 발전을 촉진하는 데 중요한 역할을 해왔습니다. 이러한 파트너십은 다양한 분야의 전문 지식을 결합하여 과제를 극복하고 차량에 탄소 섬유를 통합하는 데 박차를 가하고 있습니다.
자동차 제조업체와 탄소 섬유 제조업체의 협력
- BMW와 SGL 그룹
BMW는 SGL 그룹과 협력하여 SGL Automotive Carbon Fibers라는 합작법인을 설립했습니다. 이 파트너십은 i3와 i8 전기차 모델을 포함한 BMW 차량에 탄소 섬유 제조 공정을 개발하고 탄소 섬유 소재를 공급하는 것을 목표로 했습니다.
- 포드와 카본 레볼루션
포드는 카본 레볼루션과 협력하여 포드 GT 슈퍼카에 첨단 탄소 섬유 휠을 공동 개발하고 적용했습니다. 이 협력은 탄소 섬유 복합재를 사용하여 성능 향상, 무게 감소, 연비 개선에 중점을 두었습니다.
자동차 제조업체와 공급업체 협력
- 제너럴 모터스와 테이진
제너럴 모터스(GM)는 선도적인 탄소 섬유 제조업체인 테이진(Teijin)과 협력하여 미래 차량에 탄소 섬유 강화 열가소성 플라스틱(CFRTP) 소재를 개발하고 적용하는 방안을 모색했습니다. 이 협력은 차량 무게를 줄이고 연비를 향상시키는 것을 목표로 했습니다.
- 아우디와 도레이
아우디는 세계적인 탄소 섬유 공급업체인 도레이 인더스트리즈(Toray Industries)와 협력하여 차량 제작 시 탄소 섬유 복합재의 활용을 확대했습니다. 이 협력은 경량 탄소 섬유 소재를 활용하여 에너지 효율, 성능, 그리고 지속가능성을 개선하는 것을 목표로 했습니다.
파트너십의 중요성
자동차 제조업체, 공급업체 및 탄소 섬유 제조업체 간의 파트너십은 다음과 같은 여러 가지 이유로 필수적입니다.
- 기술 전문성 교환
협력을 통해 기술 지식과 전문성을 공유할 수 있습니다. 자동차 제조업체는 소재 개발, 제조 공정 및 품질 관리 분야에서 탄소 섬유 제조업체의 전문 지식을 활용할 수 있으며, 공급업체는 자동차 설계 요구 사항 및 생산 물류에 대한 통찰력을 얻을 수 있습니다.
- 자원 공유 및 비용 절감
파트너십은 연구 개발 시설, 장비, 지적 재산권 등 자원 공유를 가능하게 합니다. 자원을 결합함으로써 관련 당사자들은 기술 개발에 공동 투자하여 비용을 절감하고 혁신을 가속화할 수 있습니다.
- 공급망 통합
협력을 통해 자동차 제조 공정에 탄소 섬유 공급망을 원활하게 통합할 수 있습니다. 효과적인 파트너십을 통해 고품질 탄소 섬유 소재의 안정적인 공급을 보장하고, 잠재적인 병목 현상과 지연을 방지할 수 있습니다.
- 도전 극복 및 위험 완화
자동차 산업에서 탄소 섬유 도입은 높은 비용, 제조 확장성, 수리 용이성 등의 과제에 직면합니다. 협력은 자원, 기술, 전문 지식을 통합하여 이러한 과제를 해결하고, 도입 장벽을 극복하는 솔루션을 도출하는 데 도움이 됩니다.
- 채택 가속화
파트너십을 통해 탄소 섬유 적용을 위한 표준화된 제조 공정, 인증 표준 및 설계 지침 개발이 촉진됩니다. 이를 통해 탄소 섬유 도입 절차가 간소화되어 탄소 섬유가 주류 자동차 생산에 더 빠르게 통합될 수 있습니다.
요약하자면, 자동차 제조업체, 공급업체, 그리고 탄소 섬유 제조업체 간의 협력과 파트너십은 어려움을 극복하고, 혁신을 촉진하며, 자동차 산업에서 탄소 섬유 도입을 가속화하는 데 매우 중요합니다. 이러한 이해관계자들은 협력을 통해 기술, 소재 특성, 그리고 제조 공정의 발전을 촉진하고, 가볍고 효율적이며 안전한 자동차의 새로운 시대를 열어갈 것입니다.
결론
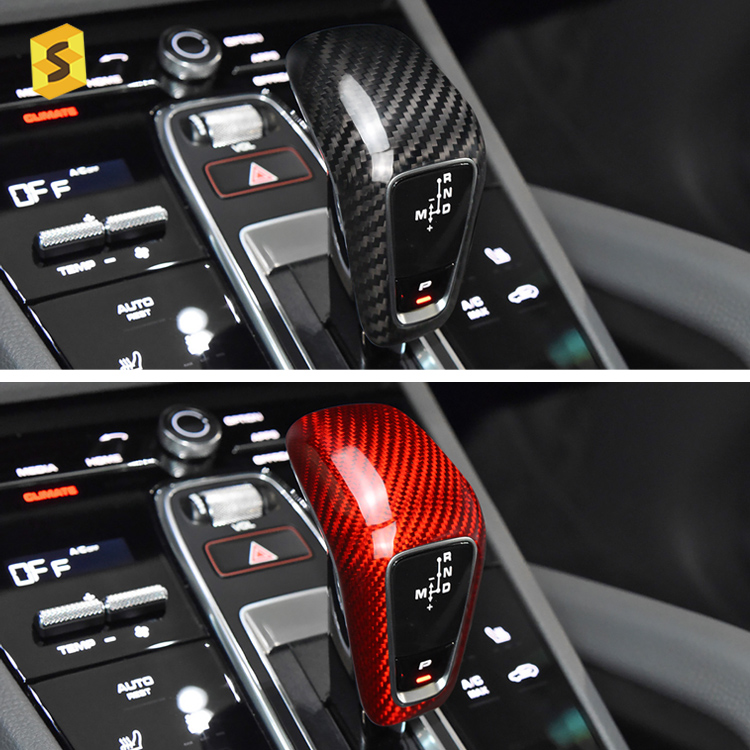
결론적으로, 탄소 섬유는 자동차 산업에 혁명을 일으키고 있습니다. 가벼운 무게, 뛰어난 안전성, 그리고 설계 유연성 덕분에 탄소 섬유는 귀중한 소재입니다. 탄소 섬유의 잠재력을 최대한 발휘하기 위해서는 지속적인 연구, 개발, 그리고 협력이 필수적입니다. 탄소 섬유를 활용함으로써 우리는 더 가볍고 안전하며 시각적으로 매력적인 차량을 개발할 수 있으며, 이를 통해 자동차 산업은 지속가능성과 고성능 기준을 향해 나아갈 수 있습니다.