Padrões de Trama | Características | Aplicações |
Ponto de tafetá | Mais leve, menor custo, menos forte | Peças não críticas para automóveis: encostos de bancos, grades de alto-falantes e acabamento do painel |
Tecido sarja | Mais leve, durável, com maior resistência e desempenho | Peças de carro sensíveis ao peso: capôs, para-lamas e spoilers |
Tecido de cetim | Menos rígido, mais demorado e caro, acabamento brilhante exclusivo e qualidade estética superior | Peças do carro onde a aparência é importante: peças do console interno, painéis das portas e espelhos laterais |
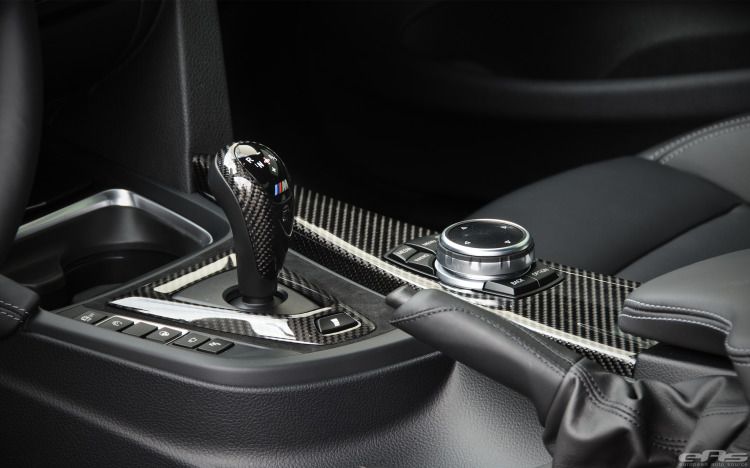
fonte: pinterest
A fibra de carbono tornou-se um material essencial na fabricação de peças de automóveis nos últimos anos. Sua propriedades incríveis de resistência e economia de peso fazem dela a melhor escolha para fabricantes de automóveis no mundo todo.
No entanto, a criação peças de carro de fibra de carbono não é tão simples quanto fabricar componentes automotivos tradicionais de metal. Padrões de trama desempenham um papel crucial no processo de fabricação de peças automotivas de fibra de carbono e afetam o desempenho, a aparência e a qualidade geral do produto acabado.
Portanto, compreender os diferentes padrões de trama das peças automotivas de fibra de carbono é essencial para designers, mecânicos e entusiastas. Neste artigo, exploraremos os diferentes padrões de trama usados na fabricação de fibra de carbono, suas características e seu impacto nas peças automotivas de fibra de carbono.
Tipos de padrões de trama
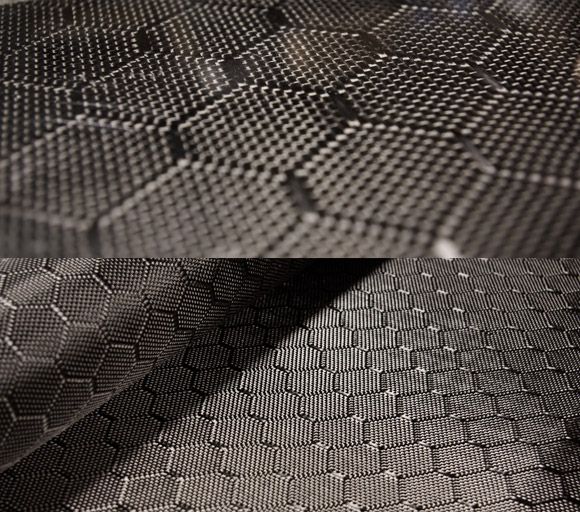
fonte: pinterest
Fabricantes de fibra de carbono Use uma variedade de padrões de trama para criar peças de automóveis. Os padrões mais comuns incluem trama simples, sarja e cetim.
Ponto de tafetá
A trama simples é o padrão de trama de fibra de carbono mais simples, com fibras perpendiculares entre si em um padrão quadriculado. Este padrão é leve mas não tão forte quanto outros padrões, tornando-o uma escolha adequada para áreas menos críticas de um interior do carro ou exterior.
Tecido sarja
O padrão de trama de sarja é um padrão diagonal mais comumente usado na fabricação de fibra de carbono. Ele fornece força e desempenho melhorados Em comparação com a trama simples, devido à sua composição diagonal. Peças automotivas que exigem maior rigidez e resistência, como capôs e para-lamas, normalmente utilizam o padrão de sarja.
Tecido de cetim
O padrão de trama de cetim é mais flexível trama com um acabamento brilhante exclusivo, tornando-o adequado para aplicações estéticas. Este padrão é complexo e demorado para ser criado, tornando-o mais caro do que outros padrões. Peças de automóveis que exigem um acabamento elegante, como um acabamentos internos do carro ou painel, pode usar o padrão de trama de cetim.
Em resumo, cada padrão de trama possui características únicas que afetam a aparência e o desempenho do produto final. Uma combinação de padrões de trama pode frequentemente ser usada em uma única peça automotiva para atingir a resistência, a rigidez e a aparência estética desejadas.
Tecido Simples: O Básico da Fibra de Carbono
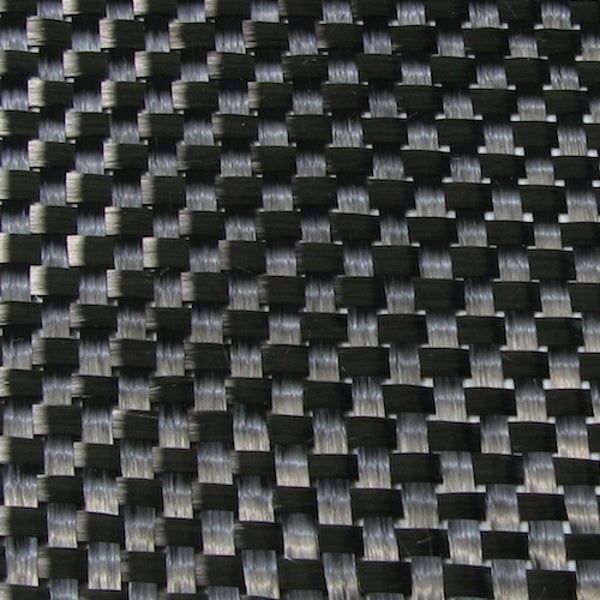
fonte: pinterest
A trama simples é o padrão de fibra de carbono mais básico e direto em uso atualmente. É composto por fibras dispostas em um padrão quadriculado, com cada fio perpendicular ao adjacente. Esse layout simples torna o padrão de trama simples o mais simples de fabricar, mas também o menos resistente.
Embora leve, o padrão de trama simples não é tão forte quanto outros padrões de trama, tornando-o mais adequado para peças automotivas não críticas onde a resistência e a rigidez não são primordiais. Alguns exemplos típicos de peças de automóveis que podem usar um padrão de trama simples incluem encostos de bancos, grades de alto-falantes e acabamento do painel.
A vantagem da fibra de carbono de trama simples é sua menor custo e peso mais leve comparado a outros padrões.
Além disso, seu textura e acabamento suaves Tornam-no ideal para peças estéticas onde a integridade estrutural não é crucial. No entanto, a resistência reduzida do padrão de trama simples o torna uma escolha menos ideal para peças de automóveis expostas a tensões externas, como impactos fortes ou altas velocidades.
Tecido Sarja: O Padrão de Resistência Aprimorado
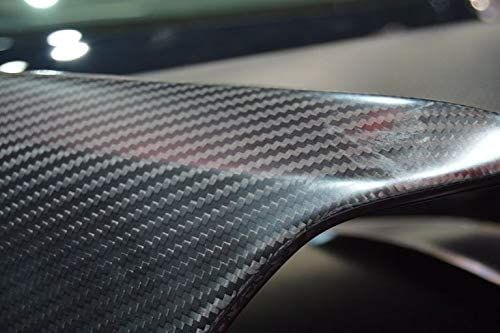
fonte: pinterest
A sarja é um padrão diagonal mais comumente usado na fabricação de fibra de carbono do que a trama simples. É composto por fibras tecidas diagonalmente, criando um padrão distinto conhecido por sua força e desempenho melhorados comparado ao padrão de trama simples.
A fibra de carbono em sarja é mais durável e oferece maior rigidez do que a fibra de carbono de trama simples. É frequentemente usado em peças de automóveis que exigem resistência, rigidez e desempenho adicionais, como capôs, para-lamas e spoilers. A fibra de carbono em sarja também é popular em carros de corrida e esportivos devido ao seu alto desempenho e durabilidade.
O padrão de trama sarja fornece maior resistência contra tensões externas em comparação com a trama simples. O arranjo diagonal das fibras permite uma melhor distribuição de forças, tornando-a ideal para peças de automóveis expostas a impactos fortes ou altas velocidades. Apesar de sua resistência aprimorada, a fibra de carbono em trama de sarja ainda é leve, tornando-o ideal para peças de carro sensíveis ao peso.
Alguns exemplos típicos de peças automotivas que utilizam o padrão de sarja incluem tampas de motor, capôs, para-lamas e spoilers. Essas peças exigem rigidez e resistência adicionais para suportar tensões externas, mantendo sua forma e propriedades aerodinâmicas.
Tecido de cetim: o padrão estético de trama
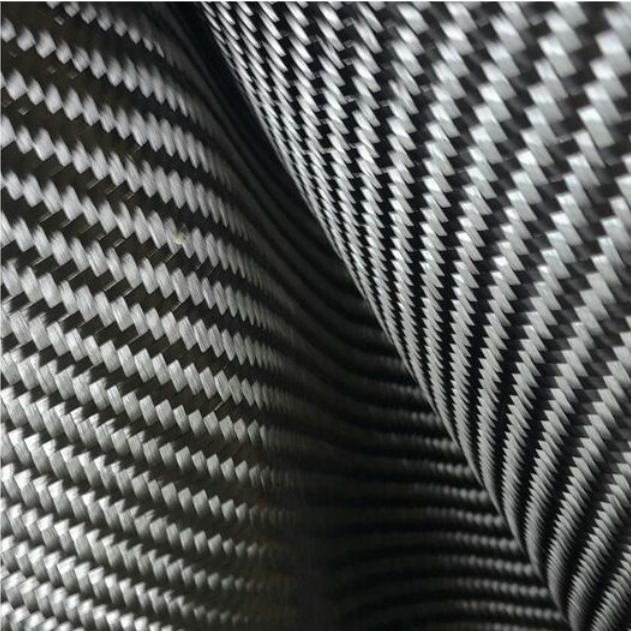
fonte: pinterest
O padrão de trama de cetim é um mais flexível tecer, conhecido por sua acabamento brilhante exclusivo e qualidade estética superiorAo contrário dos padrões de trama simples e sarja, a trama de cetim é criada pela tecelagem das fibras em um método específico que cria flutuações mais longas entre as fibras entrelaçadas. Esse padrão cria um padrão que reflete a luz de uma forma mais agradável à vista.
A técnica de tecelagem única cria um acabamento brilhante que confere à peça do carro uma aparência elegante e luxuosa. Este padrão é frequentemente usado em peças de automóveis onde a aparência é tão importante quanto a função, como acabamentos internos ou peças do console.
Uma das principais desvantagens do padrão de trama de cetim é sua complexidade, o que o torna mais demorado e caro de fabricar do que outros padrões. No entanto, o padrão de trama de cetim é menos rígido do que os padrões de trama sarja ou trama simples, tornando-o mais adequado para aplicações onde a flexibilidade é necessária.
Os fabricantes de automóveis usam o padrão de trama de cetim em peças de automóveis que exigem elegância visual e tensões funcionais mínimas, como peças do console interno, painéis das portas e espelhos laterais. Alguns carros esportivos também incorporam fibra de carbono com trama acetinada nas peças externas da carroceria para proporcionar um visual único e premium.
Padrões de combinação de tramas
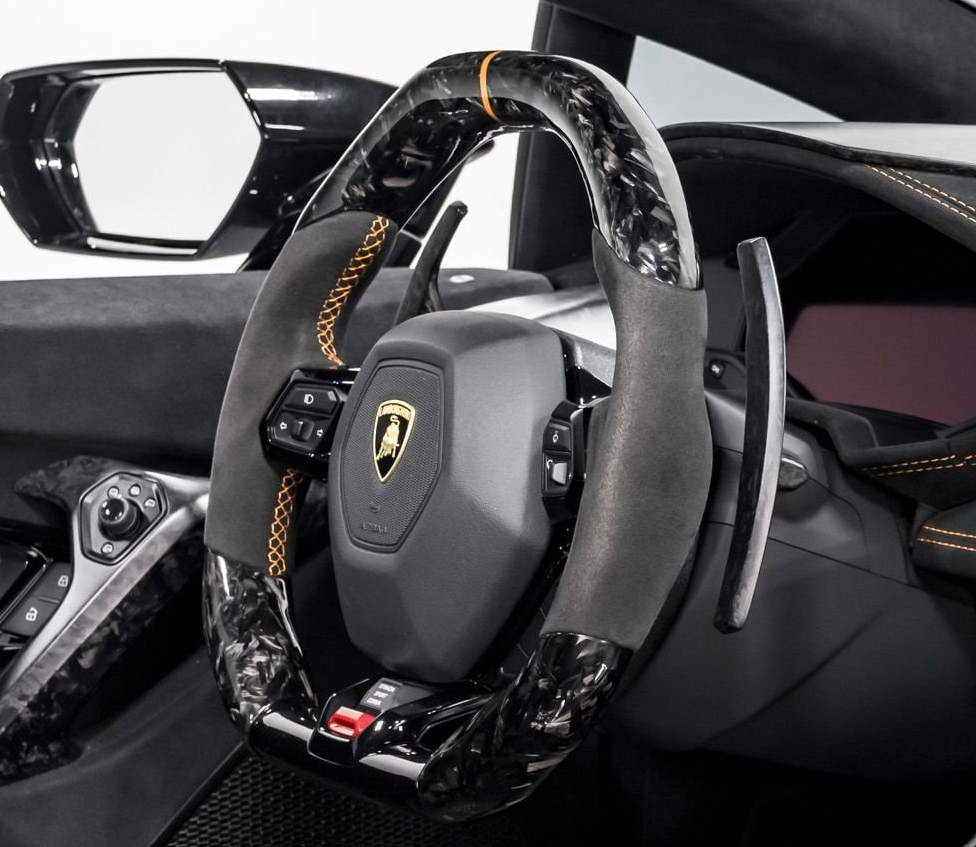
fonte: pinterest
Combinar diferentes padrões de trama em uma única peça automotiva é uma prática comum na fabricação de fibra de carbono. Ao utilizar diferentes padrões em diferentes áreas de uma peça, os fabricantes podem melhorar seu desempenho geral, estética e funcionalidade.
Uma combinação de padrões de trama pode fornecer maior resistência, rigidez e durabilidade em comparação com o uso de um padrão de trama única. Por exemplo, um fabricante pode usar um padrão de trama sarja em áreas de alta tensão, como o capô ou o spoiler traseiro, enquanto usa um padrão de trama simples nas áreas menos exigentes da peça do carro. Essa abordagem ajuda a otimizar o uso de materiais e a manter o peso total da peça.
A combinação de diferentes padrões de trama também pode melhorar a estética de uma peça. Um fabricante pode usar um padrão de trama de cetim na superfície externa de uma peça de carro, criando um efeito visual esteticamente agradável, enquanto usa um padrão de trama de sarja na parte inferior para aumentar a resistência da peça.
Escolhendo o padrão de trama correto
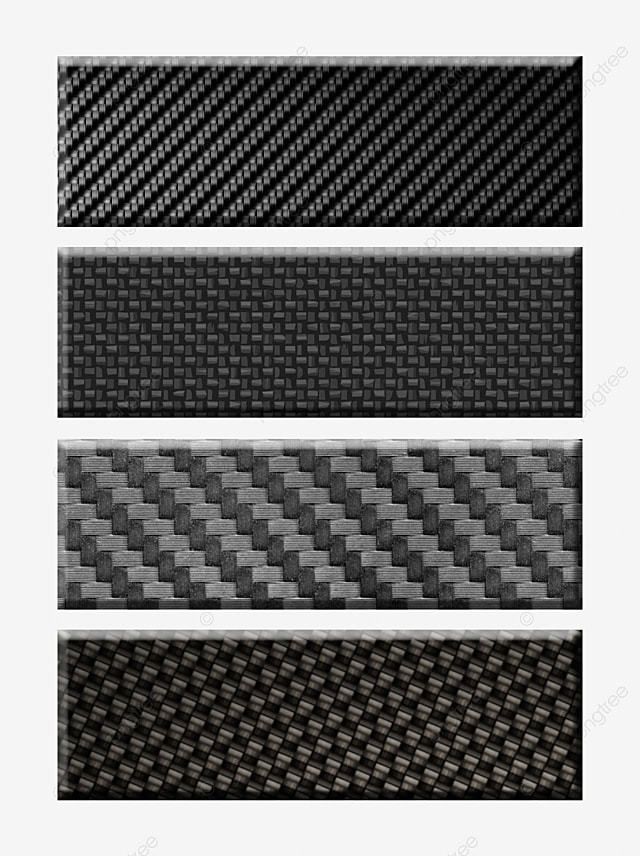
fonte: pinterest
A escolha do padrão de trama correto para uma determinada peça do carro é crucial para otimizar seu desempenho, peso e aparência. Ao selecionar um padrão de trama, vários fatores, como peso, resistência, durabilidade e custo, devem ser levados em consideração.
- Peso
A escolha de um padrão de trama leve é essencial para peças de automóveis de alto desempenho, onde a redução de peso pode melhorar a aceleração, o manuseio e a eficiência de combustível.
- Resistência e durabilidade
Para peças de automóveis que exigem maior resistência, rigidez e durabilidade, um padrão de trama mais pesado e forte pode ser mais apropriado.
- Considerações de custo
O custo é um fator importante na seleção do padrão de trama, pois padrões de trama mais complexos tendem a ser mais caros.
- Tipo de peça do carro e sua função pretendida
Outros fatores, como o tipo de peça do carro e sua função pretendida, também podem influenciar a seleção do padrão de trama. Por exemplo, peças de carro como capôs, para-lamas e spoilers exigem um padrão que ofereça resistência e leveza, enquanto as peças do console interno podem priorizar a qualidade estética em detrimento da resistência.
Conclusão
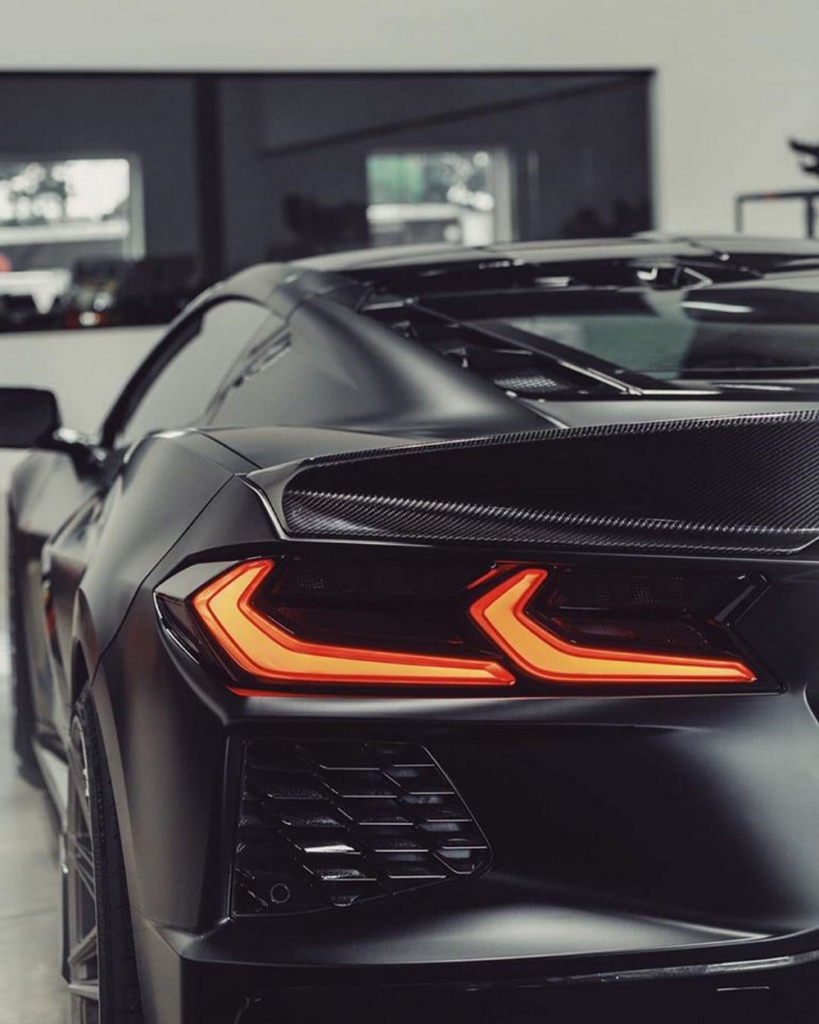
fonte: pinterest
Compreender os diferentes padrões de trama é essencial para selecionar o melhor para otimizar desempenho, peso e estética em design de produtos de fibra de carbono.
O futuro da fibra de carbono na indústria automotiva é empolgante, prometendo criar carros que sejam mais seguro, mais eficiente em termos de combustível e ainda mais atraente visualmente do que nunca. À medida que o uso da fibra de carbono continua a crescer na indústria, a compreensão dos padrões de trama continuará sendo fundamental para a criação de peças automotivas inovadoras e impressionantes.